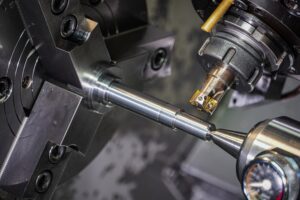
When a machine stops, everything grinds to a halt. Preventing premature failure is important to maintaining your machines and reducing downtime, so you can be as productive as possible. Knowing what causes bearing failures will help to prevent premature failures and improve your shop’s efficiency.
Causes of bearing failure
According to research in Bearing News, the main causes of bearing failure are “the inappropriate lubrication of the bearing rolling elements (approximately 80% of the cases), inadequate bearing selection (10%), improper mounting (5%), indirect failure (4%), and material defects and manufacturing errors (less than 1%).”
- Lubrication: Not using enough lubricant is a frequent cause of bearing failures, but over-lubricating or using the wrong lubrication material can cause failures, too.
- Temperature: Bearings overheating due to high speeds or inadequate lubrication is another concern.
- Contamination from the environment, like dust or sand that comes into contact with rolling elements and rings, can damage bearing surfaces.
- Abrasion: Abrasive wear can accelerate failure. Contamination or improper maintenance can cause oxidation, which damages bearings’ surfaces.
- Fatigue can also lead to microcracks and surface damage.
Preventing bearing failure
Lubrication maintenance
Proper lubrication is essential for bearing life. Bearings need the right type and quality of grease or oil, and they need it as often your machine’s manual indicates.
Different lubricants have different service lives, depending on their consistency and the material they’re made from. Maintenance intervals should be frequent enough to keep machinery running smoothly, but not so often that lubricants ooze and cause added problems.
Installation
If bearings aren’t aligned correctly when you install them, it creates load imbalance. Load imbalance leads to excessive wear and uneven heating. Carefully installing and balancing bearings extends their life
Indirect failures
Indirect failures can include operating conditions and damage during transport or storage. These indirect situations can cause defects like dents or damage to the surface of bearings or ruptured rings.
Selection
Choosing the wrong bearing for the job can lead to bearing failure. If you rule out all other sources of failure, you might need to switch to another type of bearing. Our team is expert at determining which bearings fit your needs.
Keep your machines running smoothly
Poor maintenance is the key reason for downtime. This means you have control of most factors causing time loss in your shop. Our sales engineers can help with making the right choice and the best lubrication options for that choice. We even offer re-lubrication facilities to meet your exact needs. Give us a call.